Technologies
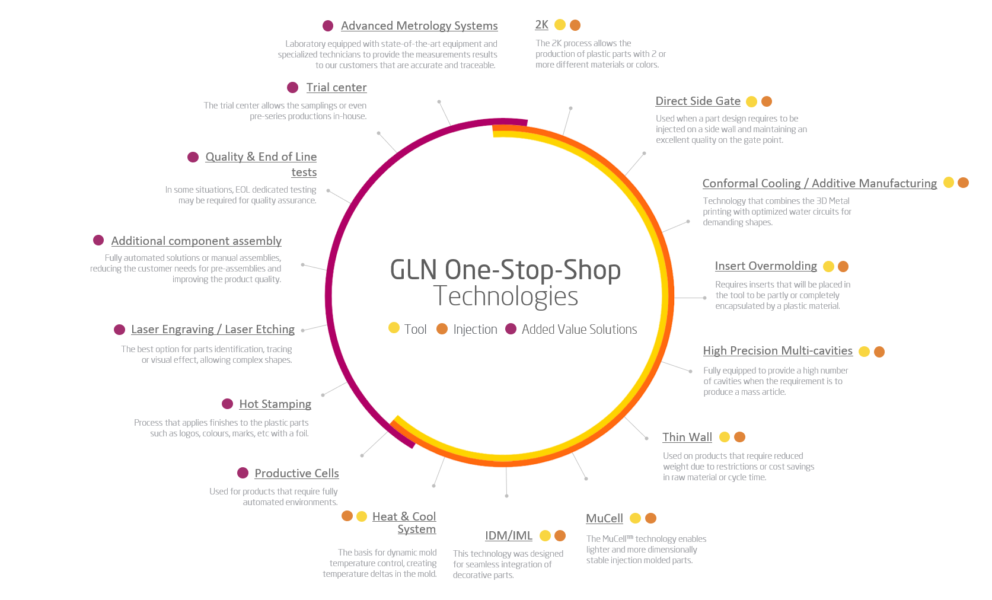
2k
Injection latérale directe
Fusion laser / additive manufacturing
Surmoulage d’inserts
Multi-cavités de haute précision
Paroi Fine
MuCell
IMD/IML
Système Chaud & Froid
Cellules de production
Marquage à chaud
Gravure au laser
Assemblage de composants supplémentaires
Tests de qualité & de fin de ligne
Centre d’essais
Systèmes de métrologie avancés
2k
Le procédé 2K permet la production de pièces en plastique avec au moins 2 matériaux ou couleurs différents.
Les principaux avantages de cette technologie sont l’intégration des deux composants, évitant l’assemblage et améliorant leur jonction, tout en réduisant les coûts de fabrication globaux. En fonction des besoins du client et de la conception de la pièce, la construction du moule sera adaptée aux technologies les plus courantes, présentées ci-dessous.
Technologies communes
- Moule rotatif/ plaque tournante
- Système Core Back
- Transfert par robot et surmoulage
- Plaque d’index
Caractéristiques principales
- Plusieurs composants dans une seule solution
- Sans temps d’assemblage
- Rentable
- Jonction améliorée
- Plus de liberté de conception
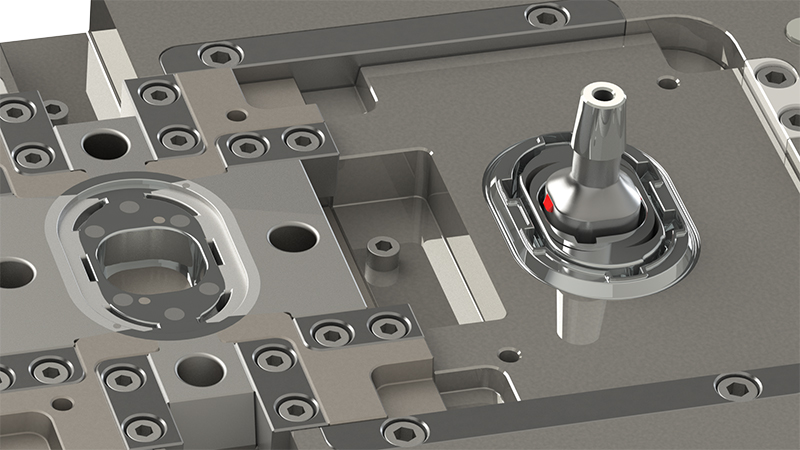
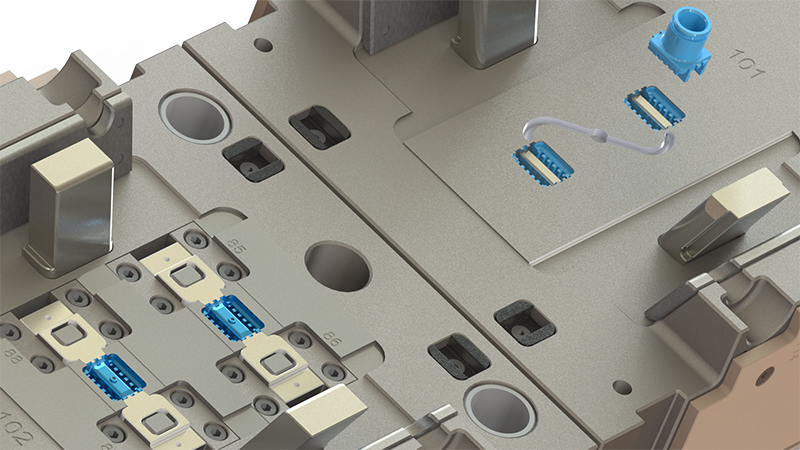
Injection latérale directe
Cette technologie est utilisée lorsqu’un concept de pièce nécessite d’être injecté sur une paroi latérale et de maintenir une excellente qualité au niveau du point d’injection. Cela se fait grâce à une injection latérale ou à une injection latérale directe par buses chaudes. GLN a recours à des systèmes d’injection des marques les plus réputées sur le marché des systèmes à canaux chauds, avec de grands avantages dans le processus d’injection.
Caractéristiques principales
- Amélioration de la qualité des pièces
- Coûts de maintenance réduits
- Contrôle amélioré de la température de processus
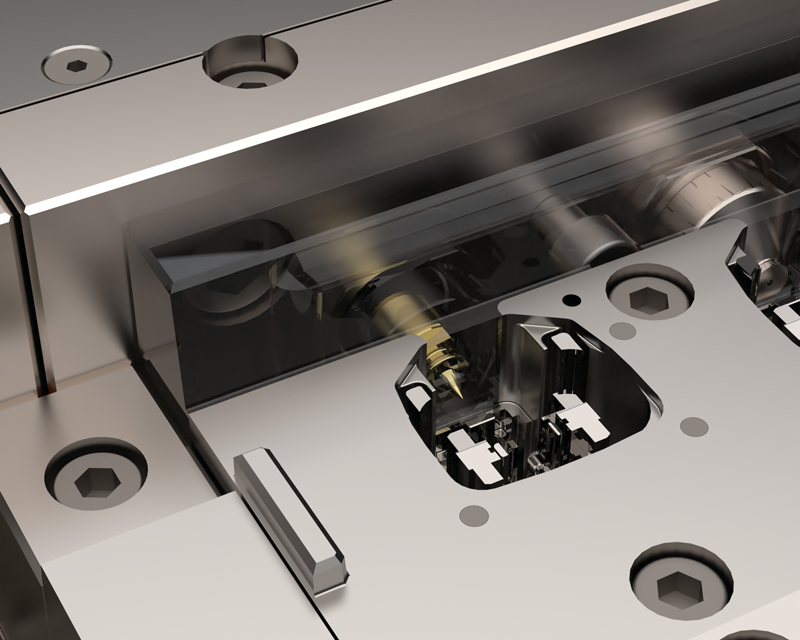
Fusion laser / additive manufacturing
La fusion laser est une technologie qui associe l’impression 3D métal, également connue sous le nom de fabrication additive (AM), pour des pièces de forme complexe avec des circuits d’eau optimisés pour des formes exigeantes. Il optimise le système de contrôle de température avec une meilleure répartition de la température tout au long des pièces en plastique, obtenant les meilleurs résultats dans le processus d’injection en termes de cycle et de qualité des pièces.
Ces processus répondent aux demandes du marché en créant des solutions rapides et en permettant des produits innovants, avec des caractéristiques mécaniques et fonctionnelles exigeantes.
Caractéristiques principales
- Meilleure répartition de la température (tout au long de la pièce en plastique)
- Liberté dans la définition de géométrie et la sélection des matériaux
- Réduction des cycles et des coûts de production
- Processus qualité des pièces flexible et amélioré
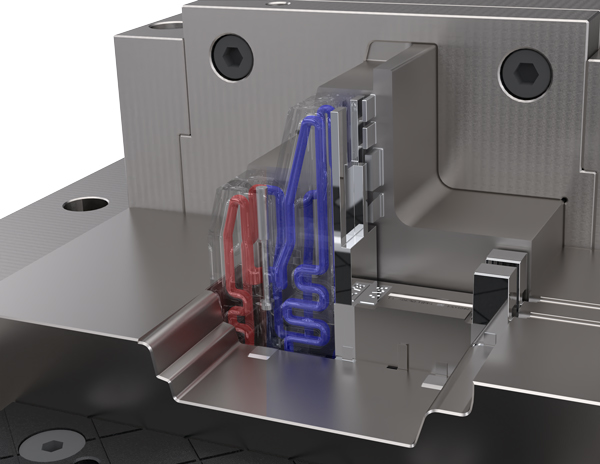
Surmoulage d’inserts
Ce procédé nécessite des inserts, tels que des vis, des bagues, ou tout autre composant, métallique ou non, qui seront placés dans l’outillage manuellement ou par un robot pour être partiellement ou totalement encapsulés par une matière plastique, produisant ainsi une pièce robuste avec intégration complète. Cette technologie peut être appliquée sur des machines d’injection verticales ou horizontales en fonction du nombre de cavités, de la typologie du produit, de la matière première et de l’emplacement de l’insert.
Caractéristiques principales
- Minimisation des coûts et du temps (avec tâches secondaires)
- Manipulation de la pièce et mouvements réduits
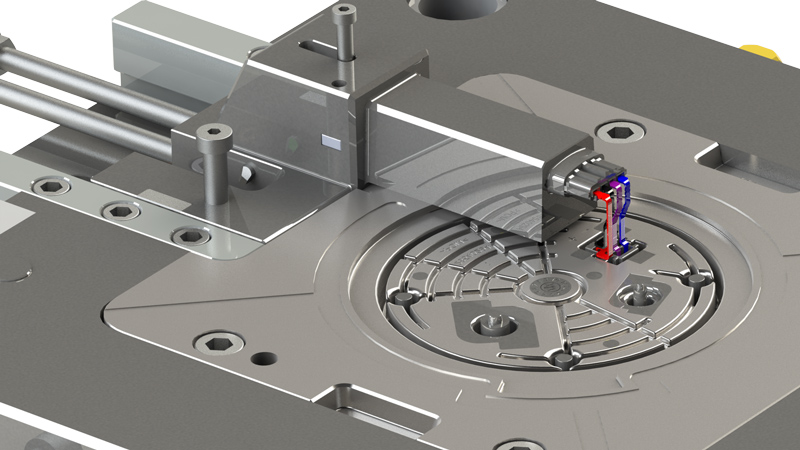

Multi-cavités de haute précision
GLN est complètement équipée pour fournir un nombre élevé de cavités lorsque l’exigence est de produire un article en masse, en ajustant les paramètres d’injection, les températures de transformation, les circuits de régulation, les temps de refroidissement pour obtenir le meilleur processus optimisé. Toutes les cavités doivent être équilibrées en termes de poids et de volume avec la répétabilité et la reproductivité des pièces en acier.
Caractéristiques principales
- Production optimisée (avec processus contrôlés)
- Grande productivité
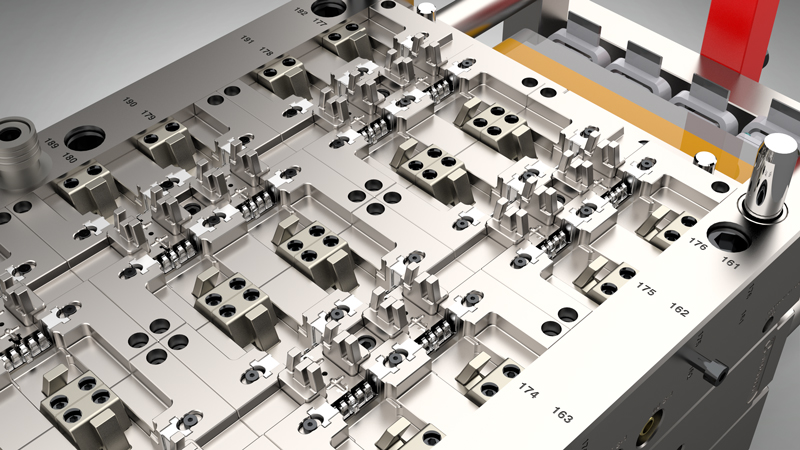
Paroi Fine
Cette technologie est utilisée pour des produits qui nécessitent un poids réduit en raison de restrictions de poids, ou des économies de coûts en matières premières ou en temps de cycle, avec une valeur ajoutée ou un impact environnemental moindre. Pour assurer la stabilité dimensionnelle, il est essentiel que le processus d’injection soit optimisé en termes de fluidité et d’efficacité. En termes d’acier, la précision dimensionnelle de chaque paroi est la clé du succès du processus d’injection.
Caractéristiques principales
- Réduction des coûts
- Réduction des temps de cycle
- Convient aux pièces à poids contrôlé
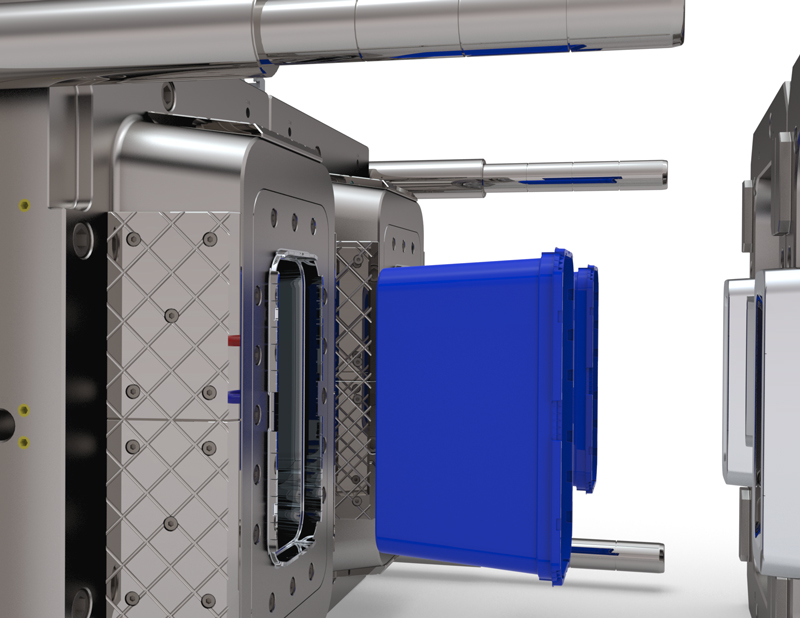
MuCell
La technologie MuCellTM appliquée à une pièce moulée a comme résultat la formation d’une couche de peau solide et d’un noyau en mousse microcellulaire qui est une structure à cellules fermées, permettant des pièces moulées par injection plus légères et dimensionnellement plus stables.
Caractéristiques principales
- Densité inférieure
- Poids réduit grâce à la liberté de conception
- Longueur d’écoulement étendue à la paroi
- Capacité de remplissage du mince à l’épais
- Faibles tensions internes
- Réduction de la déformation et des retassures
- Force de verrouillage réduite
- Économies d’énergie
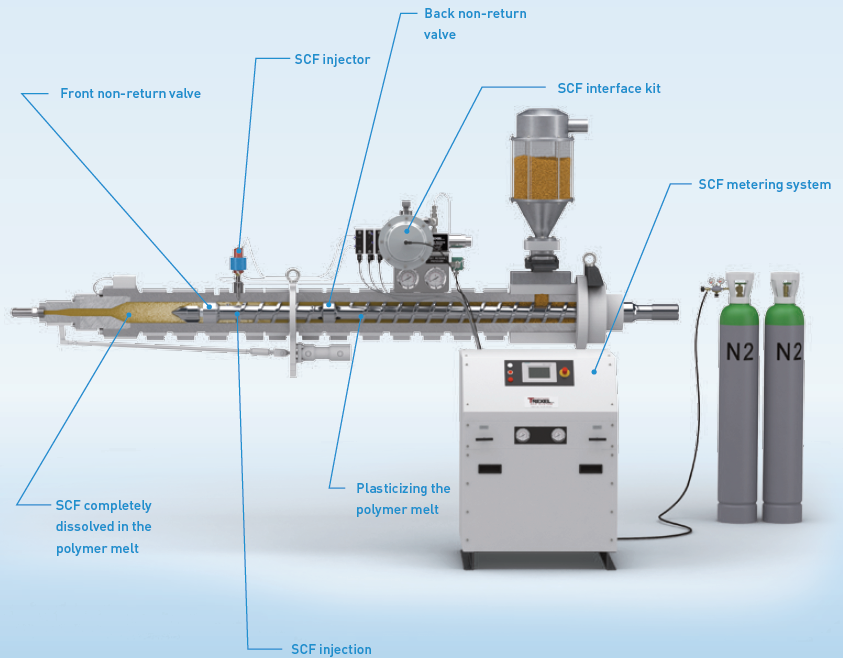
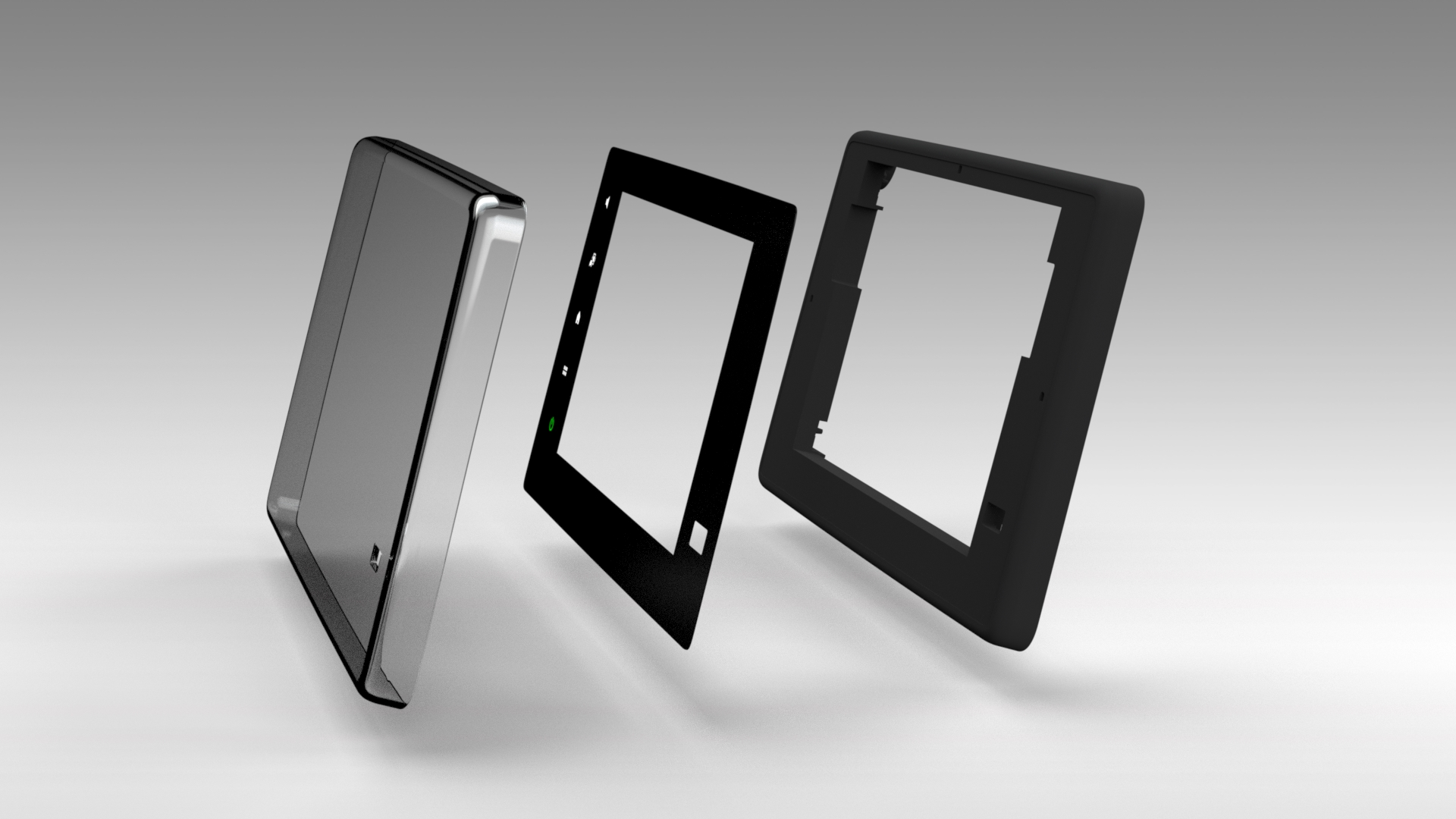
IMD/IML
Cette technologie a été conçue pour une intégration parfaite des pièces décoratives. Elle a commencé dans l’industrie de l’emballage, a intégré des graphiques complexes dans les produits sans opérations supplémentaires et s’est depuis étendue à de nombreuses industries avec l’intégration de feuilles ou d’étiquettes avec les plastiques injectés. Actuellement, elle est appliquée à l’intégration harmonieuse du plastique et de composants électroniques comme les feuilles tactiles.
Caractéristiques principales
- Intégration parfaite des pièces décoratives, du plastique et des composants électroniques
- Graphiques complexes dans les pièces
- Intégration de films ou d’étiquettes
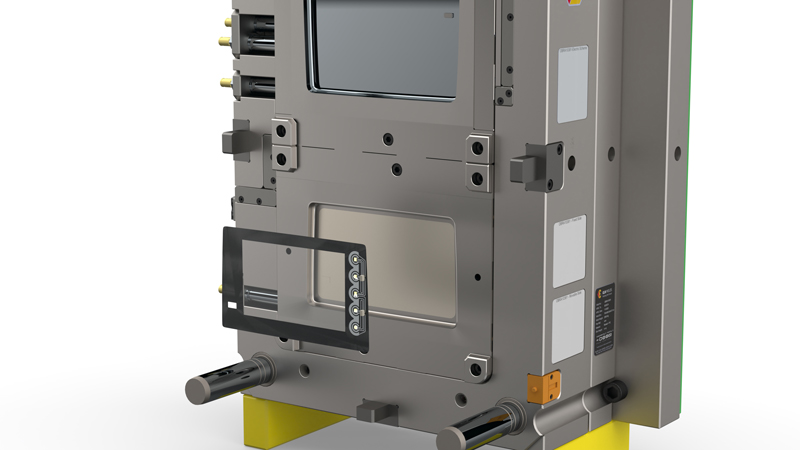
Système Chaud & Froid
Afin d’assurer une gestion complète du processus dans les pièces complexes, en évitant les problèmes tels que les défauts visuels sur les pièces esthétiques, la distorsion des pièces et l’imprécision dimensionnelle, la distribution de densité non homogène ou la vitesse et la pression d’injection élevées, l’utilisation de la technologie variothermique est parfois le choix optimal. Le contrôle de température variothermique est la base du contrôle dynamique de la température du moule, créant des deltas de température dans le moule; une interaction coordonnée entre le moule et le canal chaud et le contrôle dynamique de la température du moule; l’opérateur peut influencer directement le moulage de surface et le comportement de solidification grâce à deux circuits de contrôle de température avec des niveaux de température différents. La commutation entre ces circuits permet un chauffage ou un refroidissement ciblé.
Caractéristiques principales
- Chauffage et refroidissement rapides
- Pression et vitesse d’injection plus faibles
- Qualité de surface uniforme
- Force de verrouillage inférieure
- Augmentation de la stabilité dimensionnelle
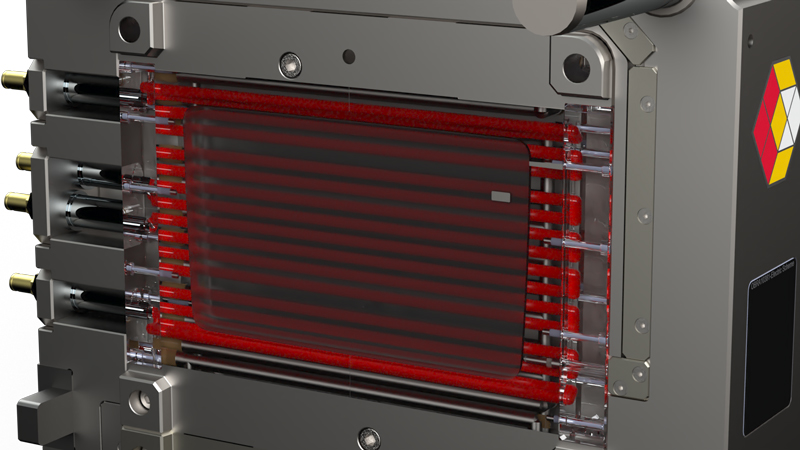
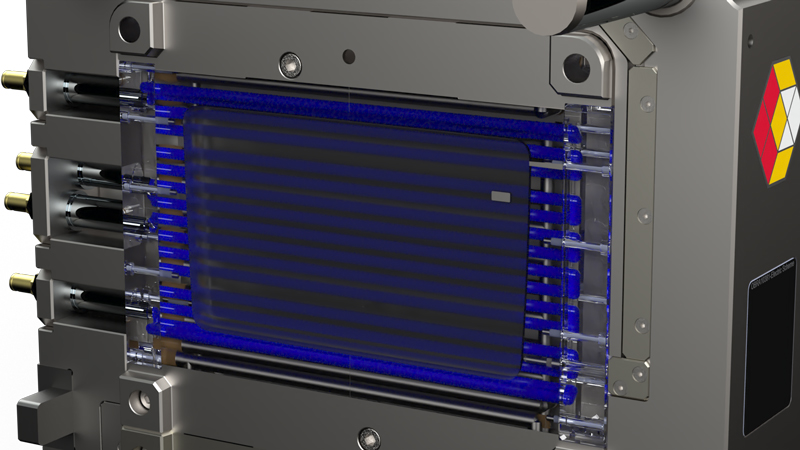
Cellules de production
Cette solution est utilisée pour les produits qui, en raison de leur complexité, de leurs exigences ou de leurs volumes, nécessitent des environnements entièrement automatisés avec une interaction minimale ou nulle de l’opérateur.
Caractéristiques principales
- Processus entièrement automatisé
- Interaction minimale ou inexistante avec l’opérateur
- Idéal pour les pièces complexes
- Contrôle dimensionnel continu
- Vérification de la présence d’inserts
- Assemblage automatisé de composants
- Opérations complémentaires automatisées telles que tampographie, soudure, marquage, gravure laser, etc…
- Tests et contrôles de fin de ligne automatisés tels que les tests d’étanchéité, les tests Hipot, le marquage à chaud, etc.
- Approbation ou rejet automatique des pièces
- Nettoyage des pièces (système d’air)
- Emballage automatisé
- Contrôle statistique continu
- Analyse de la dégradation des processus en ligne
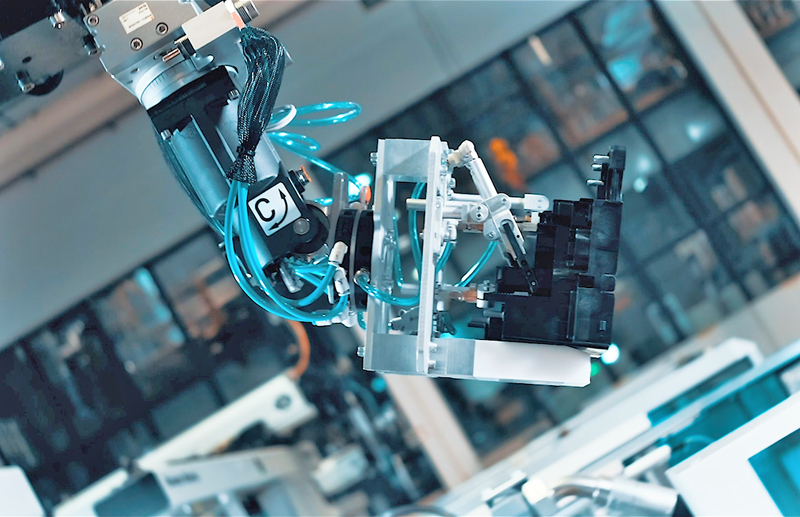

Marquage à chaud
Le processus d’estampage à chaud est un processus qui applique des finitions sur des pièces en plastique, telles que des logos, des couleurs, des marques, etc. avec une feuille. Chez GLN, ce processus est intégré aux Cellules Productives, permettant la réduction des coûts de manutention, réduisant le temps consommé par le processus; le contrôle de vision à 100% permet une inspection rapide qui sépare les pièces non conformes des pièces conformes. De plus, le processus d’ionisation dans les cellules élimine la contamination qui pourrait survenir lors de l’estampage.
Caractéristiques principales
- Uniformisation des couleurs
- Processus propre (sans pré-préparation des encres)
- Instantané (il n’y a pas besoin de temps de séchage)
- Permet des arrêts et des démarrages lorsque nécessaire
- Adhérence constante d’une pièce à l’autre
- Maniement plus sûr aussi bien pour l’opérateur que pour le consommateur final (pas d’utilisation de produits chimiques)
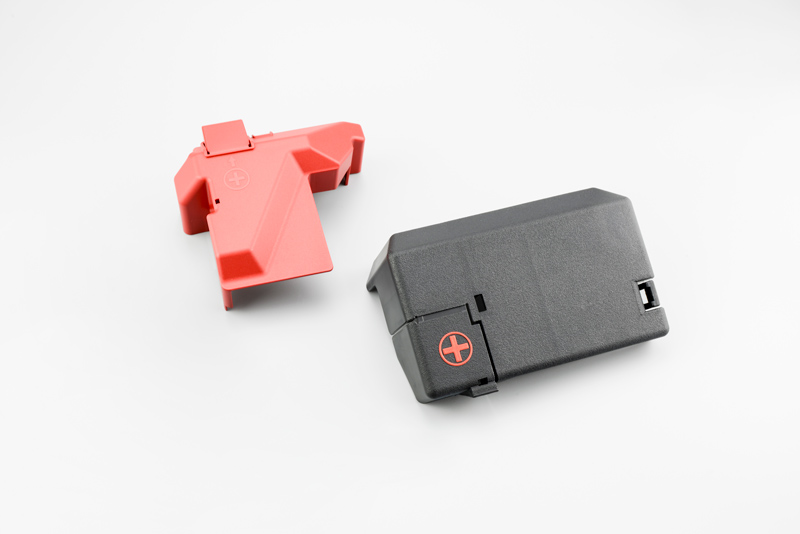
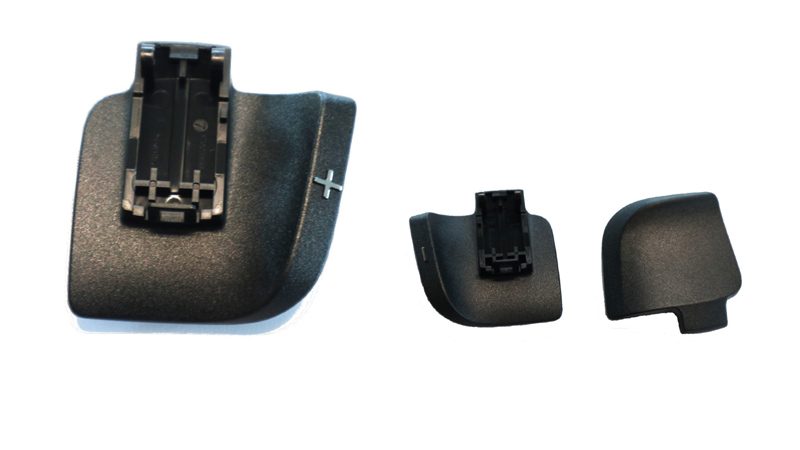
Gravure au laser
Lorsque des pièces nécessitent des opérations de gravure pour l’identification, le traçage ou l’effet visuel des pièces, l’utilisation de la gravure au laser est la meilleure option, permettant des formes complexes allant des numéros de pièce aux codes QR. Cette technologie peut également être utilisée pour créer des effets de rétroéclairage sur les boutons et autres surfaces.
Caractéristiques principales
- Personnalisation pour ID, traçage de l’effet visuel
- Gravure de formes complexes telles que les codes QR
- Effets de rétroéclairage (sur les boutons ou autres surfaces)
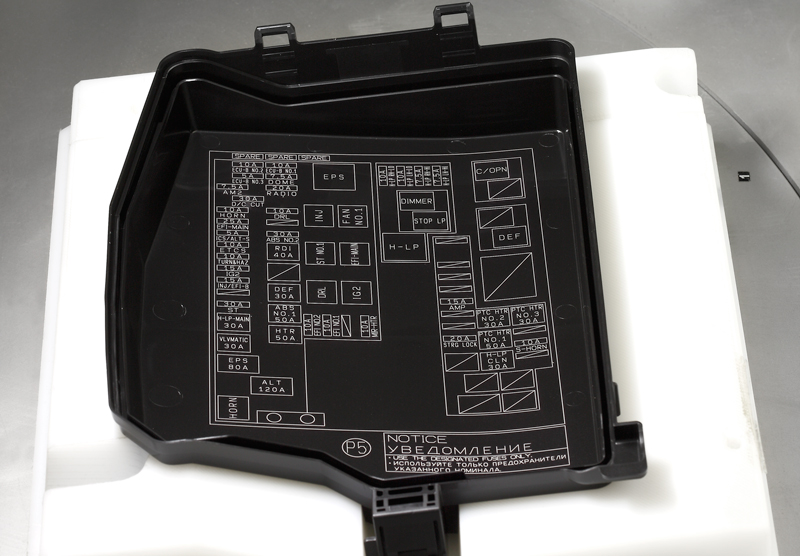
Assemblage de composants supplémentaires
De nombreux produits nécessitent l’assemblage de composants supplémentaires après injection, tels que: montage de pièces en plastique, pressage de composants, soudures, des joints toriques ou d’autres inserts. GLN peut fournir ces services via des solutions entièrement automatisées ou des assemblages manuels, réduisant les besoins des clients en pré-assemblages et améliorant la qualité du produit. Nous pouvons également fournir des produits complètement assemblés et emballés aux clients qui en ont besoin.
Caractéristiques principales
- Réduction des besoins des clients en matière de pré-assemblage
- Amélioration de la qualité du produit
- Possibilité d’assemblage complet et/ ou de produits emballés

Tests de qualité & de fin de ligne
Chaque fois qu’un produit a des fonctionnalités spéciales telles que les exigences d’étanchéité, exigences de conductivité électrique ou de barrière, niveau de transparence spécifique, conformité électrique plc ou autre, l’ajout d’un équipement de test dédié fin de ligne peut être nécessaire pour assurer 100% de garantie qualité aux pièces.
Caractéristiques principales
- Équipement de test dédié fin de ligne
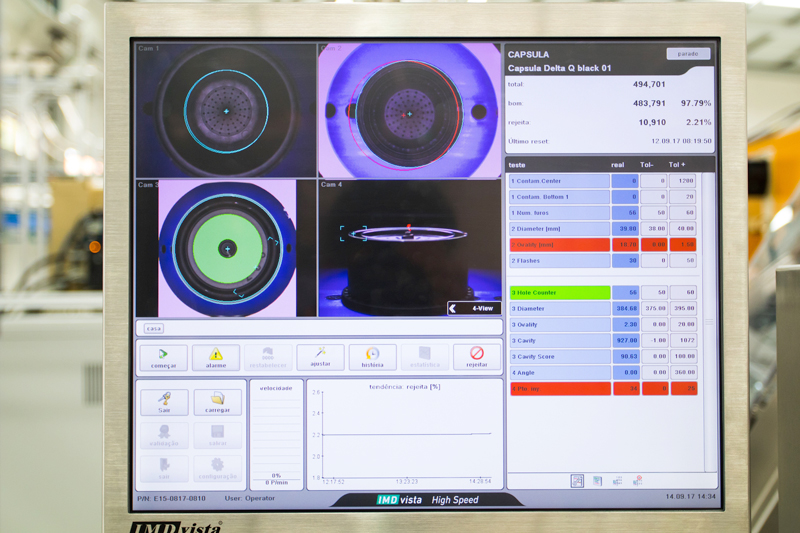
Centre d’essais
GLN a créé son propre centre d’essais, équipé de 6 presses à injection pour une gamme de tonnage entre 80 à 160 tonnes, ce qui permet l’échantillonnage en interne, voire des productions en pré-série pour nos clients, garantissant le contrôle total du processus. Ce procédé permet la validation des travaux entrepris lors des phases de fabrication des nouveaux outillages.
Caractéristiques principales
- 6 presses à injection
- Gamme de tonnage: 80-160 tonnes
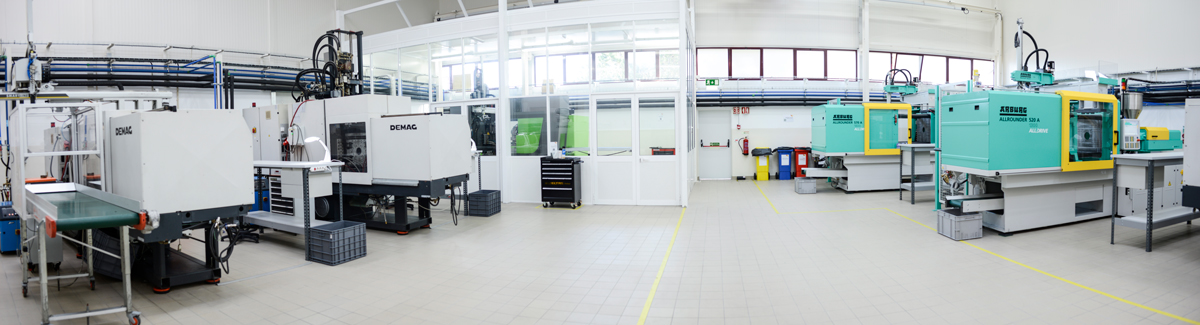
Systèmes de métrologie avancés
GLN a mis en place un laboratoire équipé d’équipements de pointe et de techniciens disposant du savoir-faire et de l’expérience nécessaires pour fournir à nos clients des résultats de mesures précis et traçables.
Les équipements clé disponibles pour ces processus sont: CMM; numérisation 3D (GOM); mesure de la rugosité de surface; projecteur de profil; microscope et tomographie.
La tomographie est une méthode de mesure nettement plus rapide que les méthodes de mesure traditionnelles et capte de nombreux points de mesure aussi bien sur les géométries externes que sur les géométries internes de la pièce en plastique, céramique ou composite, sans qu’il soit nécessaire de couper ou de détruire la pièce. Cette machine détecte près de 3 millions de pixels pour une reconnaissance détaillée avec le plus haut degré de précision dans un fichier STL, passible d’être utilisé dans plusieurs logiciels de contrôle dimensionnel.
Caractéristiques principales
- Analyse de pièces plastiques et rapports
- Contrôle dimensionnel (scanner 2D et 3D)
- Tomodensitométrie
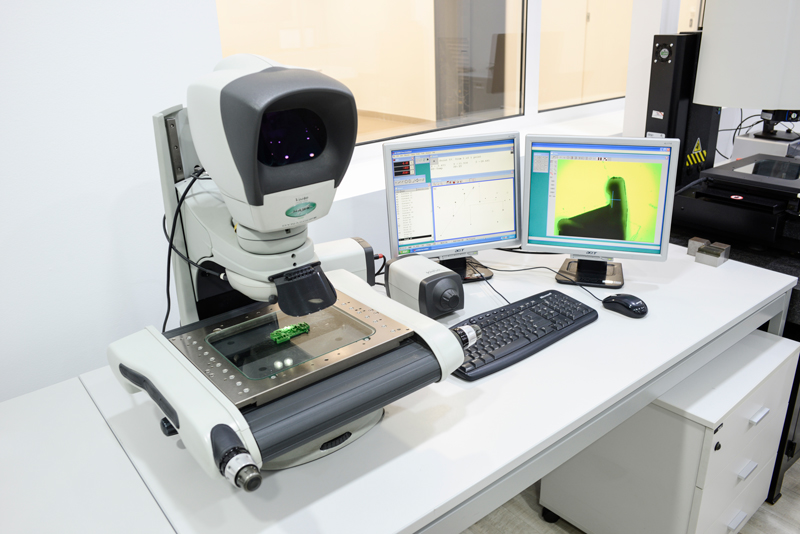
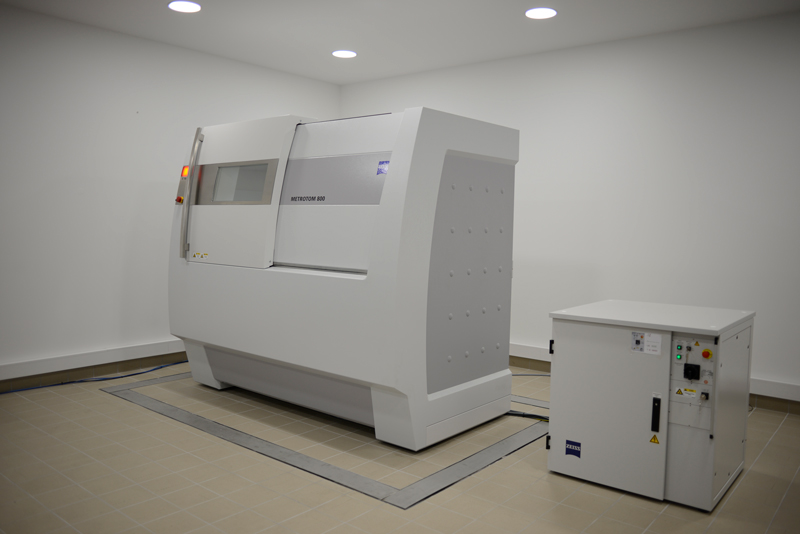
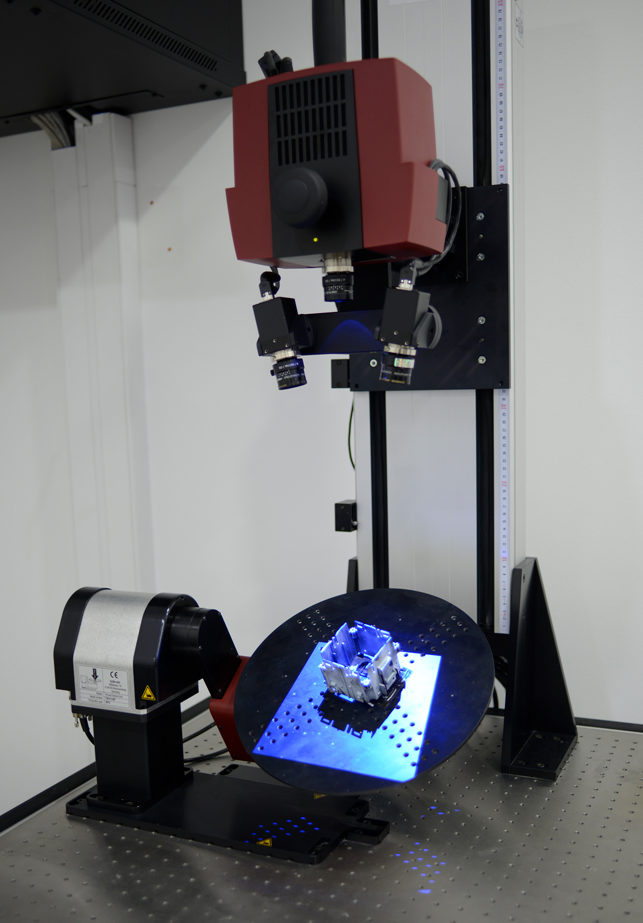