Technologies
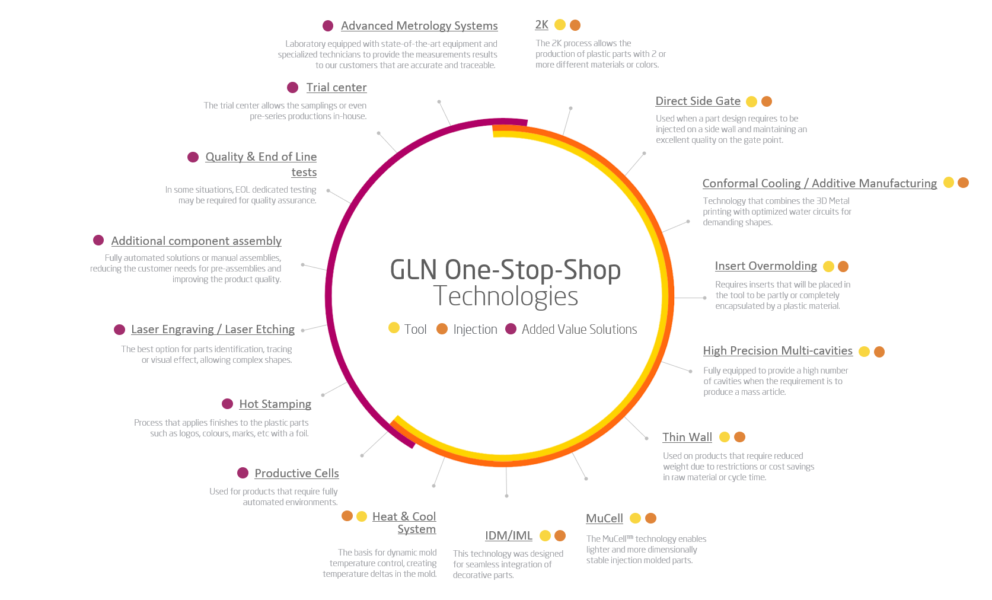
2k
Direct Side Gate
Conformal Cooling / Additive Manufacturing
Insert Overmolding
High-precision Multi-cavities
Thin Wall
MuCell
IMD / IML
Heat & Cool System
Productive Cells
Hot Stamping
Laser Engraving / Laser Etching
Additional component assembly
Quality & End of line tests
Trial Center
Advanced metrology systems
2k
The 2K process allows the production of plastic parts with two or more different materials or colors.
The main advantage of this technology is the integration of both these components, avoiding assembly and improving the connection while reducing the overall manufacturing costs. Depending on the client’s needs in terms of plastic molding process & industrial metrology and the part design, the mold construction will be adopted following the most common technologies shown below.
Common Technologies
- Rotating Mold / Rotating Plate
- Core Back System
- Robot Transfer and Over Molding
- Index Plate
Main Features
- Multiple components in a single solution
- No assembly time
- Cost-effective
- Improved connection
- More design freedom
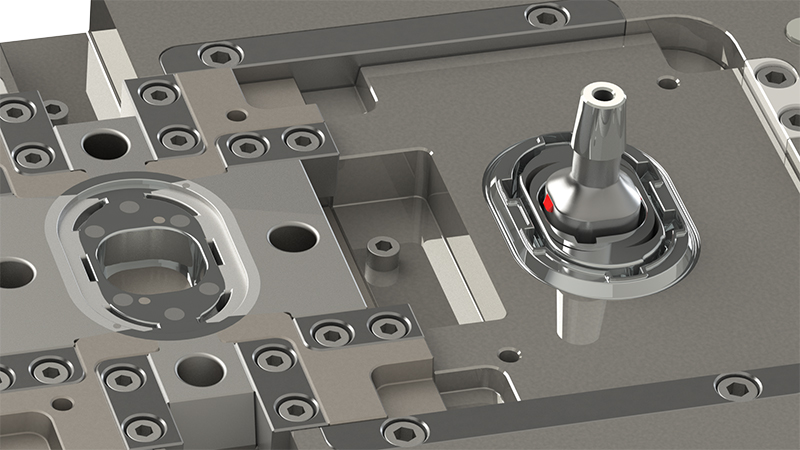
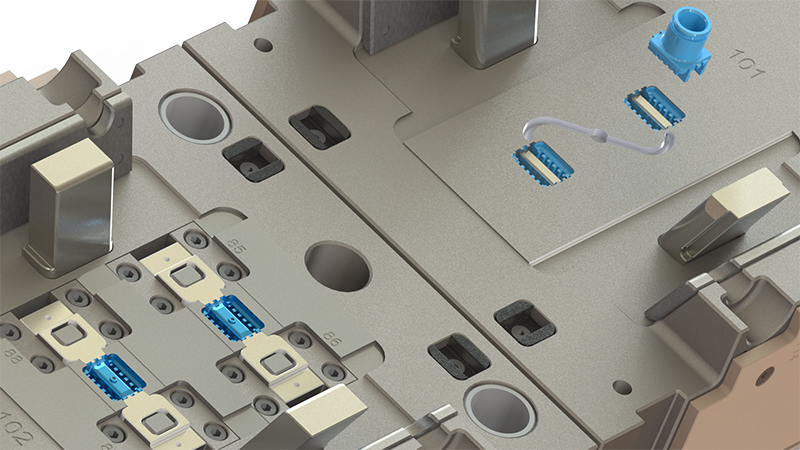
Direct Side Gate
This technology is used when a part design requires to be injected on a side wall and maintaining an excellent quality on the gate point. This is achieved through lateral gating or direct side gate hot drops. GLN uses injection systems of the most reputable brands in the market of Hot Runner Systems with great benefits in the injection process.
Main Features
- Improved part quality
- Reduced maintenance costs
- Improved process temperature control
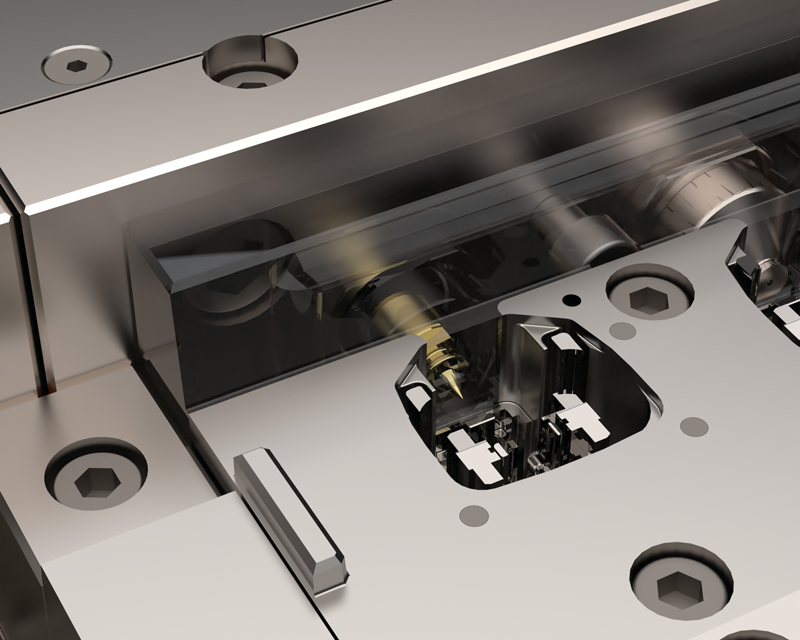
Conformal Cooling / Additive Manufacturing
Conformal cooling is a technology that combines 3D Metal Printing, also known as additive manufacturing (AM), with optimized water circuits for demanding and complex shaped parts. It optimizes the temperature control system with better temperature distribution along with the plastic parts, obtaining the best results in the injection process in terms of cycle and part quality.
These processes respond to market demands by generating rapid solutions and enabling innovative products with challenging mechanical and functional characteristics.
Main Features
- Better temperature distribution (along the plastic part)
- Freedom in geometry and material selection
- Reduced cycles & production costs
- Flexible and better part quality process
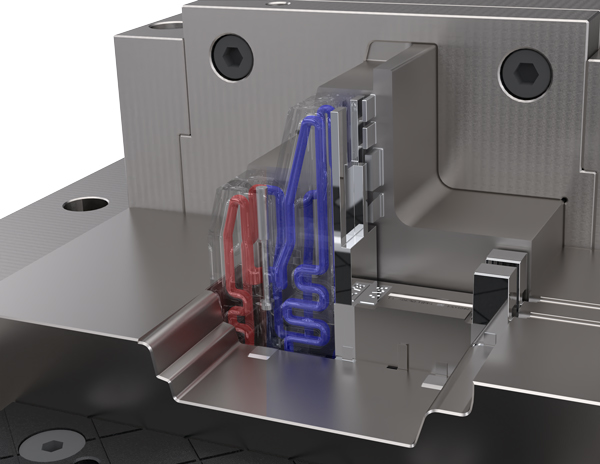
Insert Overmolding
This process requires inserts, such as screws, washers, or any other component, metallic or not, that will be placed in the tool manually or by a robot to be partly or completely encapsulated by a plastic material, obtaining this way a robust part with full integration. This technology can be applied on vertical or horizontal injection machines depending on the number of cavities, typology of the product, and on insert raw material and location.
Main Features
- Cost & time minimization (with secondary tasks)
- Reduced part handling & movements
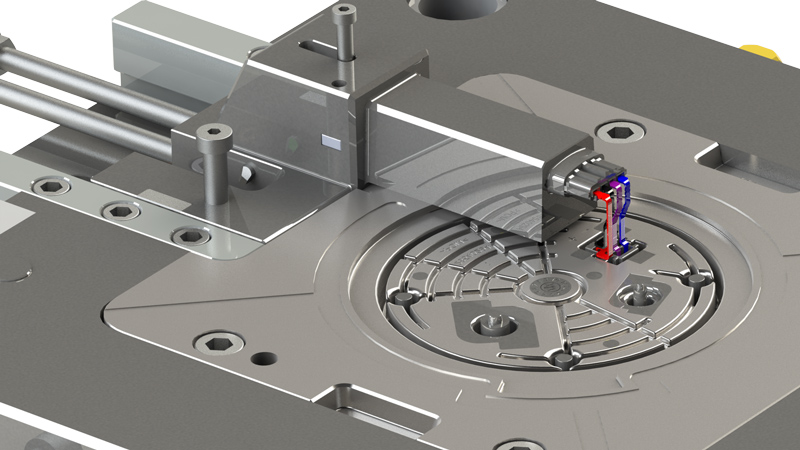

High-precision Multi-cavities
GLN is fully equipped to provide a high number of cavities when the requirement is to produce a mass article, adjusting injection parameters, processing temperatures, water lines, and cooling times to get the best-optimized process. All cavities must be balanced in terms of weight and volume achieved with repeatability and reproductivity of the steel parts.
Main Features
- Optimized production (with controlled processes)
- High productivity
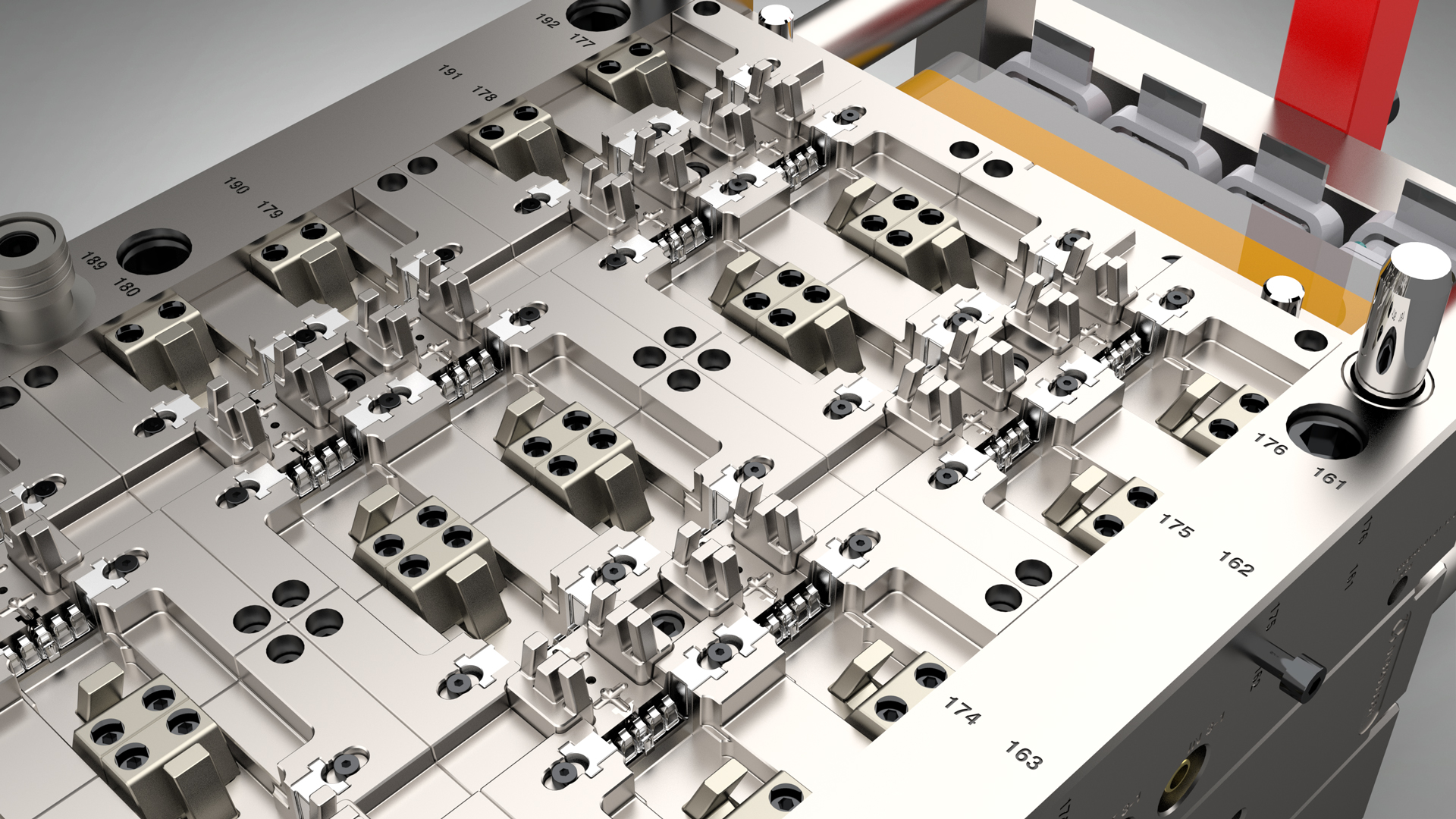
Thin Wall
This technology is used on products that require reduced weight due to weight restrictions, or cost savings in raw materials or cycle time, with the added value or smaller environmental impact. To assure dimensional stability it is the key for the injection process to be optimized on fluidity and effectiveness. In terms of steel, the dimensional precision in each wall is the key for success in the injection process.
Main Features
- Cost-saving process
- Reduced cycle times
- Fit for weight controlled parts
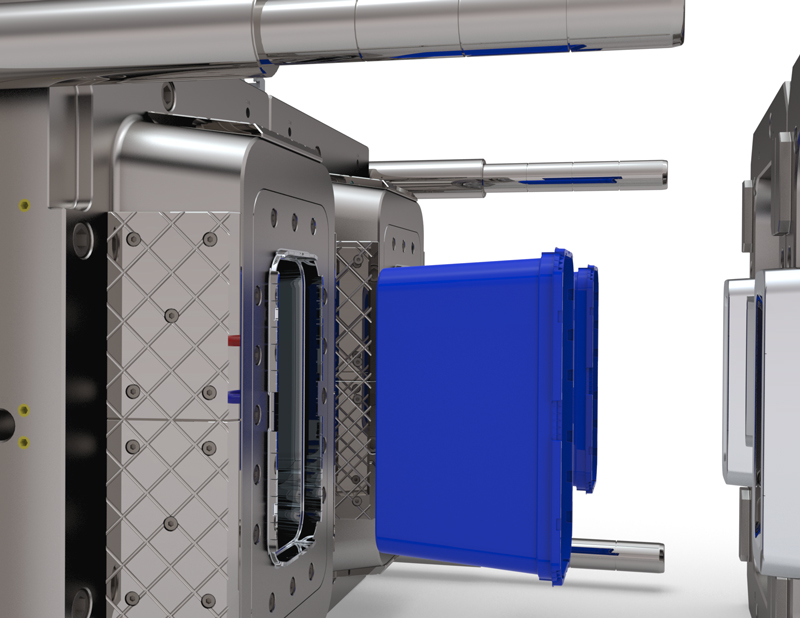
MuCell
The MuCelltm technology applied to a molded part leads to a solid skin layer and microcellular foamed core which is a closed-cell structure, enabling lighter and more dimensionally stable injection molded parts.
Main Features
- Lower density
- Reduced weight through design freedom
- Expanded flow length to wall
- Ability to fill thin to thick
- Low molded-in stress
- Reduced warp & sink
- Reduced clamp force
- Energy savings
- Reduced cycle time
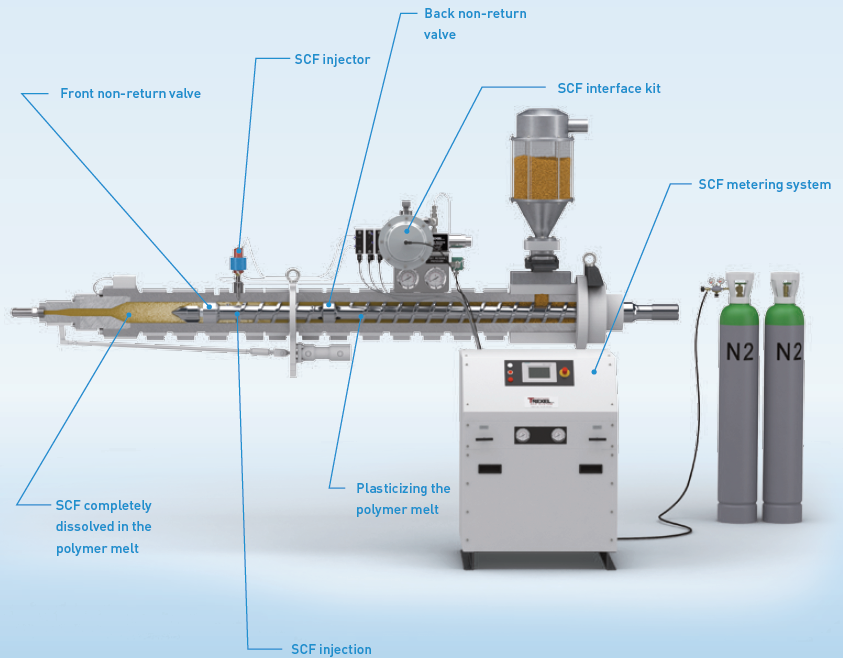
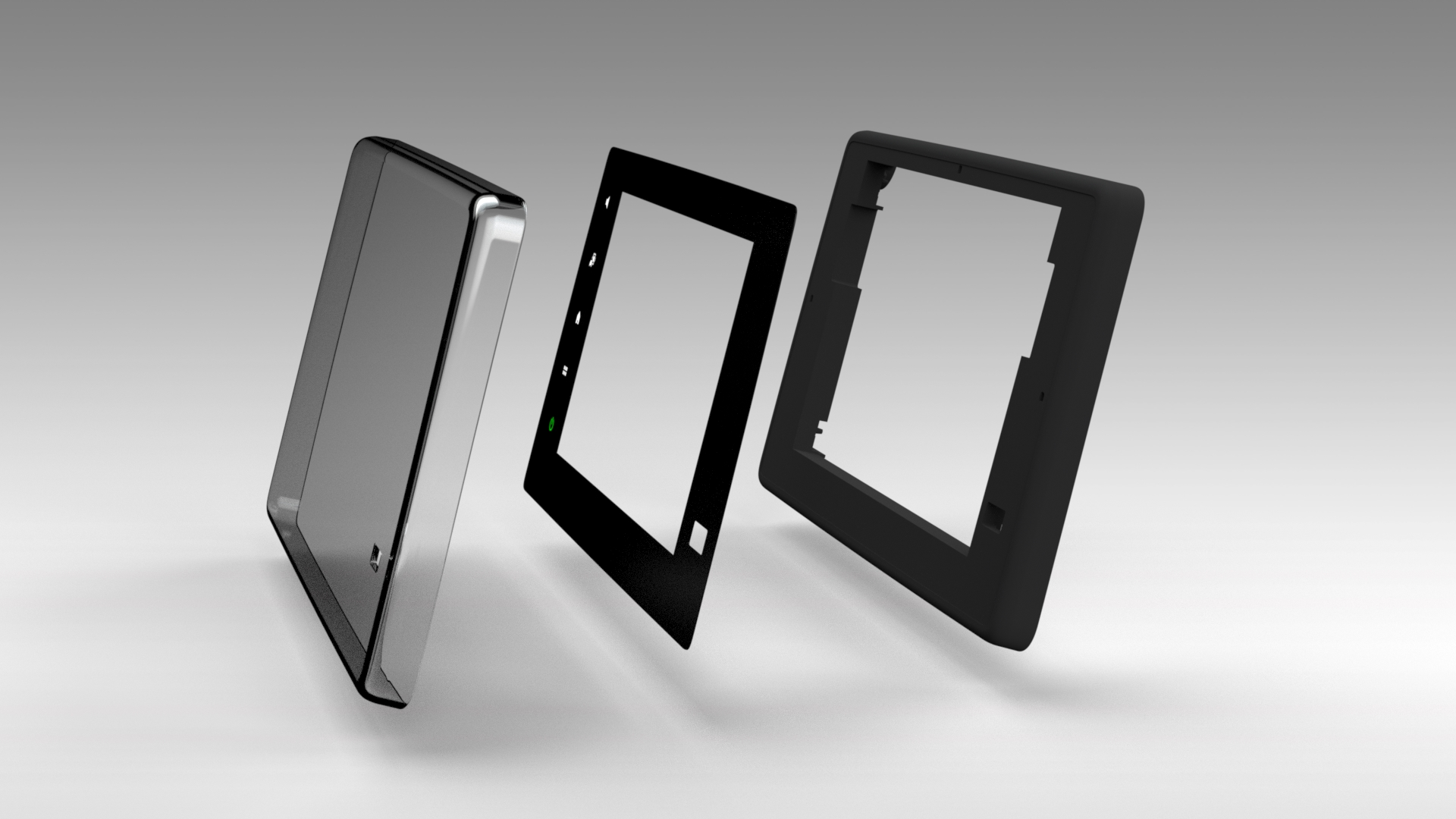
IMD / IML
This technology was designed for seamless integration of decorative parts. It started in the packaging industry, integrating complex graphics into the products without additional operations and has since expanded through many industries with the integration of foils or labels with the injected plastics. Currently it is being applied to seamless integration of plastic and electronics such as touch sensitive foils.
Main Features
- Seamless integration of decorative parts, plastic and electronics
- Complex graphics into parts
- Integration of foils or labels
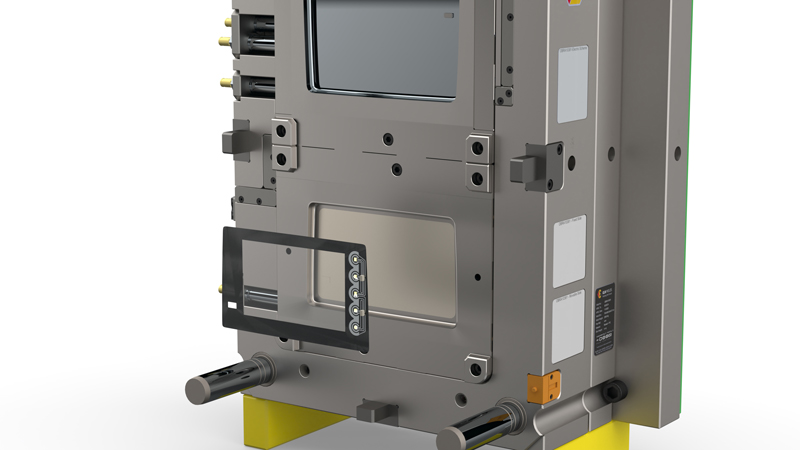
Heat & Cool System
In order to assure full process management in complex parts avoiding issues as visual defects on aesthetic parts, part distortion and dimensional inaccuracy, inhomogeneous density distribution or high injection speed and pressure, the use of Variothermal technology is sometimes the optimal choice. The Variothermal temperature control is the basis for dynamic mold temperature control, creating temperature deltas in the mold; coordinated interaction between the mold and the hot runner, and dynamic mold temperature control. The user can directly influence the surface molding and the solidification behavior by using two temperature control circuits with different temperature levels. Switching between these circuits allows for heating or targeted cooling.
Main Features
- Rapid heating and cooling
- Lower injection pressure and speed
- Uniform surface quality
- Lower clamping force
- Dimensional stability increase
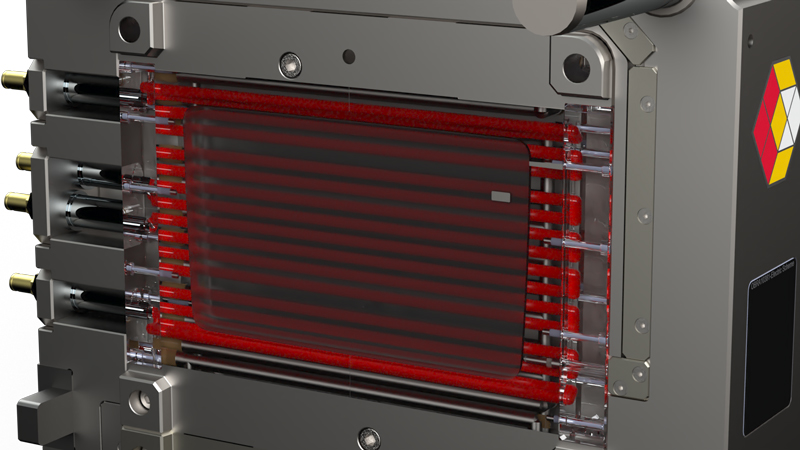
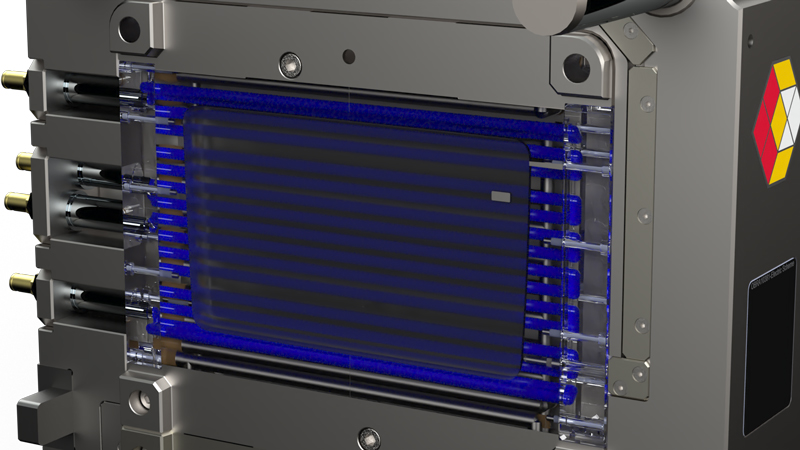
Productive Cells
This solution is used for products that due to their complexity, requirements or volumes need fully automated environments with minimal or no operator interaction.
Main Features
- Fully automated process
- Minimum or no operator interaction
- Ideal for complex parts
- Continuous dimensional control
- Insert existence verification
- Automated assembly of components
- Automated additional operations such as pad printing, welding, marking, laser etching, etc
- Automated end of line tests & controls such as leak proof testing, hipot testing, hot stamping, etc
- Automatic approval or rejection of parts
- Parts cleaning (air system)
- Automated packaging
- Continuous statistical control
- Online process degradation analysis
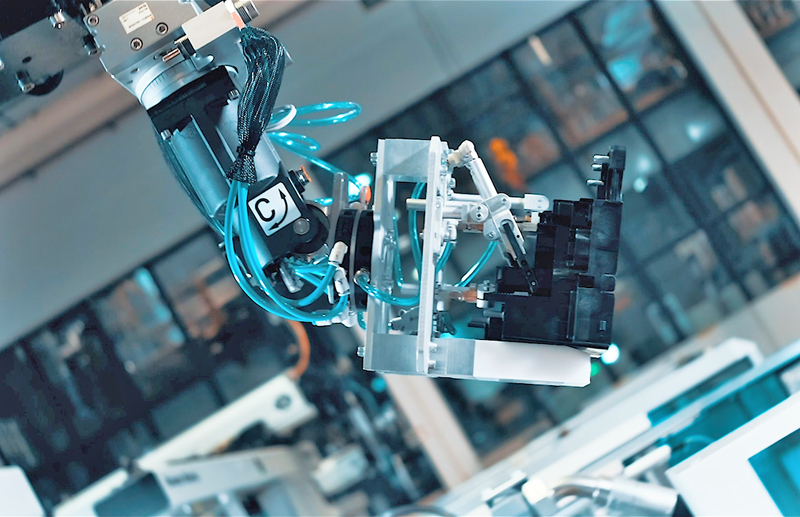

Hot Stamping
The Hot Stamping process is a process which applies finishes to plastic parts, such as logos, colors, marks and so on with a foil. At GLN, this process is integrated with the Productive Cells, permitting the reduction of handling costs, and reducing the time consumed with the process. The 100% vision control allows a quick inspection separating the non-conformal parts from the conformal ones. Also, the ionization process in the cells eliminates the contamination that could occur during the stamping.
Main Features
- Standardization of colors
- Clean process (without pre-preparation of inks)
- Instant (doesn’t need drying time)
- Allows stops and start-up whenever needed
- Constant adherence from one part to another
- Safer handling for both the operator and the final consumer (no use of chemicals)
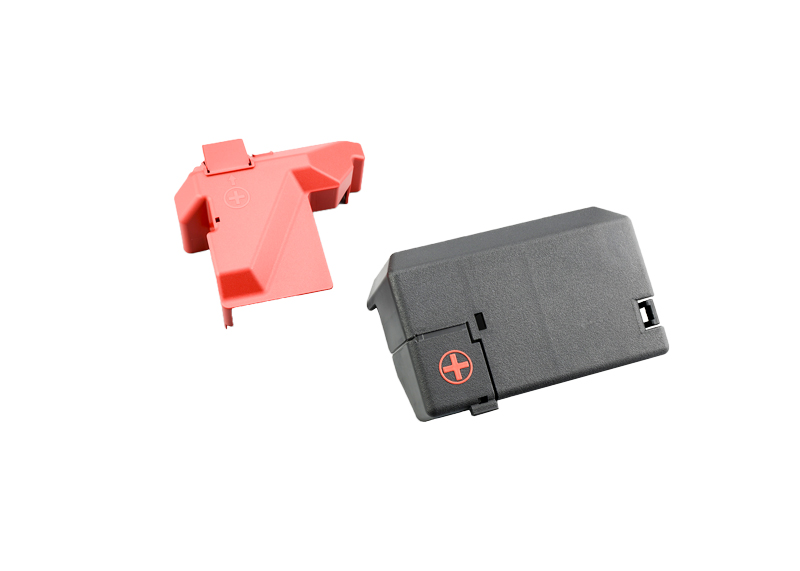

Laser Engraving / Laser Etching
When parts require engraving operations for part identification, tracing, or visual effect the use of laser engraving is the best option, allowing for complex shapes from part numbers to QR codes. This technology can also be used to create backlight effects on buttons and other surfaces, and is an important complement to the plastic molding process & industrial metrology.
Main Features
- Customization for ID, tracing of visual effect
- Engraving of complex shapes such as QR codes
- Backlight effects (on buttons or other surfaces)
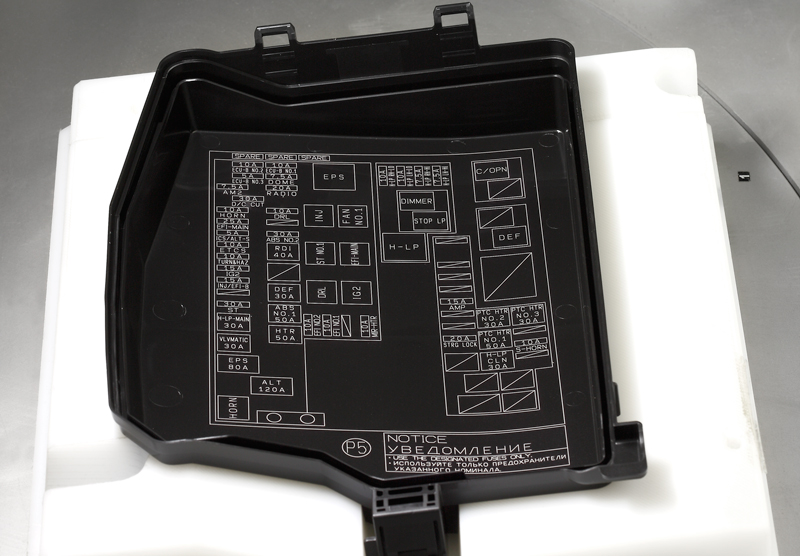
Additional component assembly
Many products require the assembly of additional components after injection such as the mounting of plastic parts, press fitting components, weldings, o-rings or other inserts. GLN can provide these services, as part of its plastic molding process & industrial metrology, through fully automated solutions or manual assemblies, reducing the customer needs for pre-assemblies and improving the product quality. We can also provide full assembly and packaged products for customers that require so.
Main Features
- Reduction of customer needs for pre-assembly
- Improved product quality
- Possibility for full assembly and/or packaged products

Quality & End of line tests
Whenever a product has special functions such as leak-proof requirements, electrical conductivity or barrier requirements, specific transparency level, electrical plc conformity or other, the addition of an EOL dedicated testing equipment may be required to guarantee 100% part quality assurance.
Main Features
- EOL dedicated testing equipment
- 100% part quality assurance
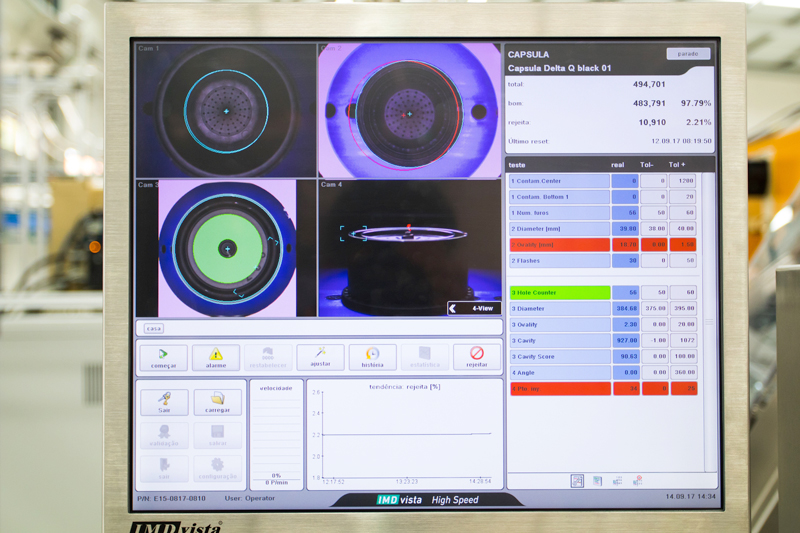
Trial Center
GLN has created its own trial center equipped with 6 injection machines with a tonnage ranging from 80 to 160 ton that allows in-house samplings, or even pre-series productions for our customers, guaranteeing total process control. This process allows the validation of the work developed during the manufacturing phases of the new molds.
Main Features
- 6 injection machines
- Tonnage range: 80–160 ton
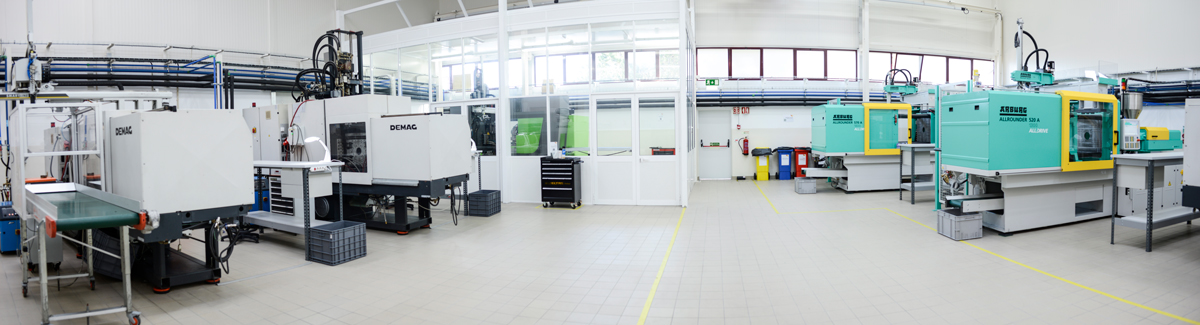
Advanced metrology systems
GLN has settled a laboratory equipped with state-of-the-art equipment and technicians that have the know-how and experience to provide measurements results for our customers that are accurate and traceable, thus highly improving the overall quality of our plastic molding process & industrial metrology.
The key equipment that is available for these processes is: CMM; 3D scanning (GOM); surface roughness measurement; profile projector; microscope and tomography.
The tomography is significantly faster than traditional measuring methods and captures numerous measurements points in the external, but also on the internal geometries of the plastic, ceramic or composite part, with no need to cut or destroy the part. This machine detects almost 3 million pixels for detailed recognition with the highest degree of accuracy into a STL file that can be used in several dimensional controls software.
Main Features
- Plastic parts analysis & reports
- Dimensional control (2D & 3D scanner)
- Computed tomography
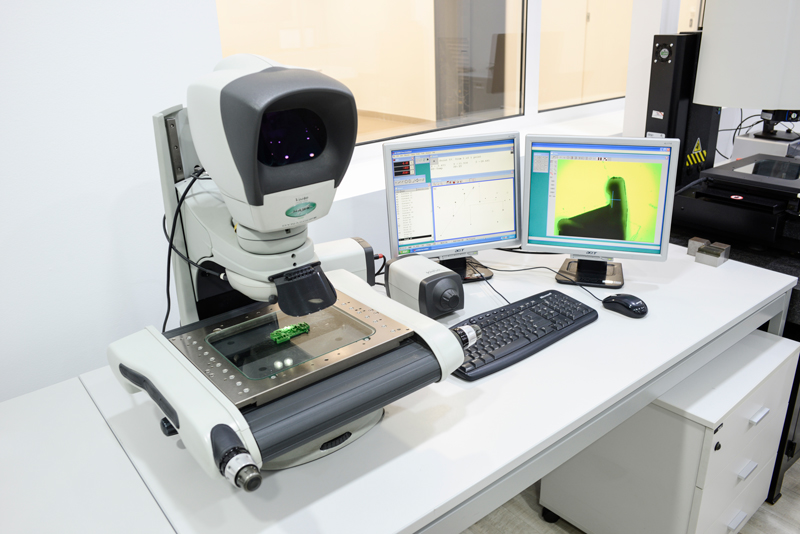
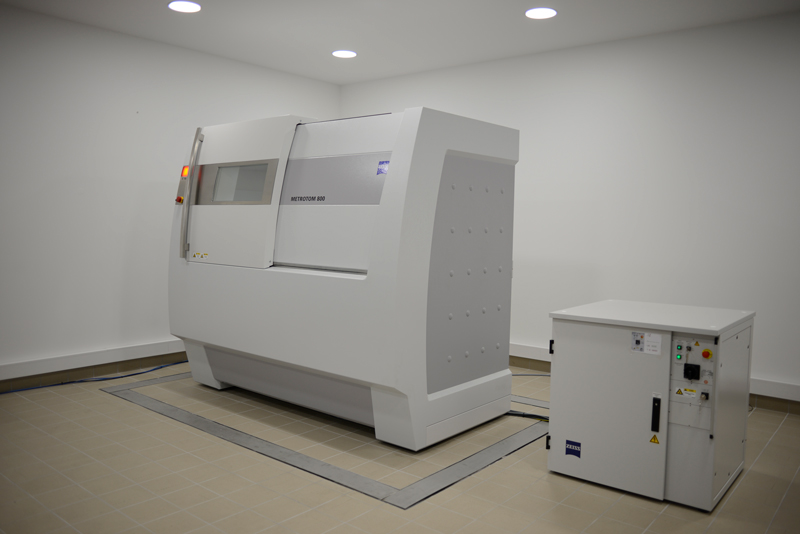
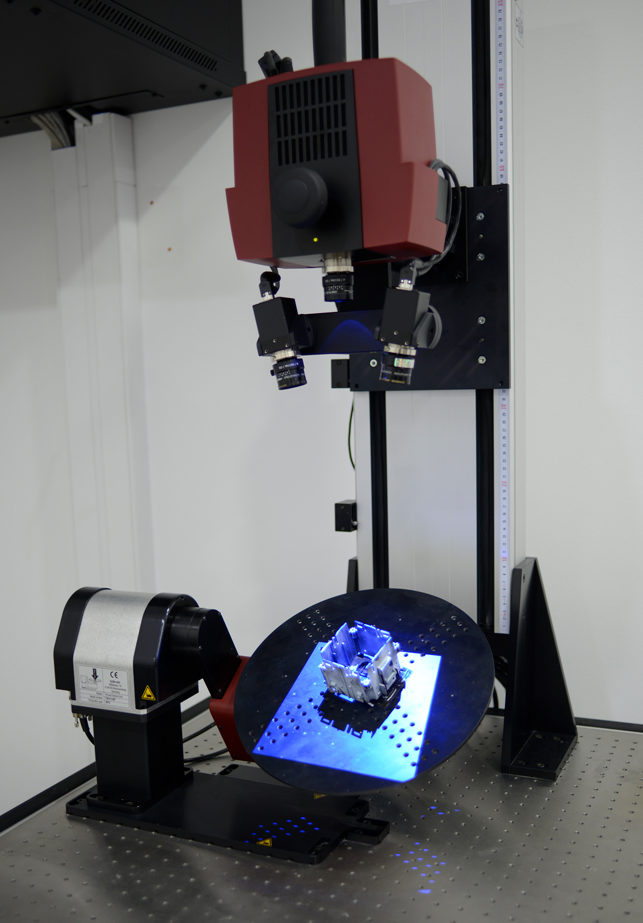